一、对进给系统的要求 进给运动是以保证刀具与工件相对位置关系为目的,被加工工件的轮廓精度和位置精度都受到进给运动的传动精度、灵敏度和稳定性的直接影响。 进给运动是数字控制系统的直接控制对象。对于闭环控制系统,还要在进给运动的末端加上位置检测系统,并将测量的实际位移反馈到控制系统中,以使运动更准确。进给运动的机械结构必须具备以下几个特点。 1. 运动件间的摩擦阻力小 2. 消除传动系统中的间隙 3. 传动系统的传动精度和刚度高 4. 减小运动惯量,具有适当的阻尼 二、传动齿轮副 1. 设计传动齿轮副应考虑的问题 使丝杠、工作台的惯量在系统中占有较小的比重。 使高转速低转矩的伺服驱动装置的输出变为低转速大转矩。 在开环系统中可归算所需的脉冲当量。 速比分配及传动级数对传动的转动惯量和执行件的失动的影响。 2. 消除传动齿轮间隙 由于数控机床进给系统的传动齿轮副存在间隙,在开环系统中会造成进给运动的位移值滞后于指令值;反向时,会出现反向死区,影响加工精度;在闭环系统中,由于有反馈作用,滞后量可得到补偿,但反向时会造成伺服系统产生振荡而不稳定。为了**数控机床伺服系统的性能,减少或消除齿轮间隙方法有刚性调整法和柔性调整法。 三、丝杠螺母副 数控机床的进给运动链中,将旋转运动转换为直线运动的方法很多,本节只介绍滚珠丝杠螺母副和静压丝杠螺母副。 (一)滚珠丝杠螺母副 1.工作原理和特点 1) 原理 丝杠和螺母上都有圆弧形面的螺旋槽, 在工作过程中,滚珠既自转又循环滚动, 丝杠和螺母间为滚动摩擦。 2) 特点: 摩擦损失小,传动效率高,可达0.90~0.96; 预紧后,可完全消除间隙,**传动刚度和精度; 摩擦阻力小; 平稳、无爬行; 磨损小、精度保持好、寿命长; 发热量小,适应高速运动; 具有运动的可逆性:螺母、丝杠均可作主动件或从动件。故不能自锁、丝杠立式使用需增加制动装置。 2. 结构类型 按滚珠循环方式可分为以下两种: 1) 外循环(滚珠通过螺母外表面返回) 外循环方式中的滚珠在循环返向时,离开丝杠螺纹滚道,在螺母体内或体外作循环运动。如图7-7所示插管式外循环,弯管两端插入与螺纹滚道相切的两个孔内,弯管两端部引导滚珠进入弯管,形成一个循环回路,再用压板2和螺钉将弯管固定。插管式外循环结构简单,制造容易,但径向尺寸大,且因为滚道接缝处很难做得平滑,影响滚珠滚动平稳性,甚至发生卡珠现象,噪声较大。
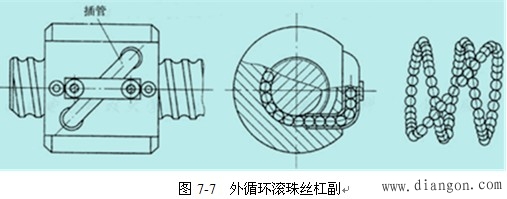 2) 内循环(滚珠通过螺母内表面返回) 内循环方式的滚珠在循环过程中始终与丝杠表面保持接触。如图7-8所示,在螺母2的侧面孔内装有接通相邻滚道的反向器4,利用反向器引导滚珠3越过丝杠1的螺纹顶部进入相邻滚道,形成一个循环回路,称为一列。一般在同一螺母上装有2~4个反向器,并沿螺母圆周均匀分布。内循环方式的优点是滚珠循环的回路短、流畅性好、效率高、螺母的径向尺寸也较小,但制造精度要求高。 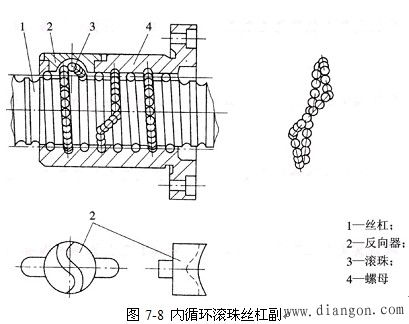 3. 滚珠丝杠螺母副的预紧 滚珠丝杠螺母副预紧的基本原理是使两个螺母产生轴向位移,以消除它们之间的间隙和施加预紧力。图7-9所示结构是通过修磨垫片的厚度来调整轴向间隙。这种调整方法具有结构简单可靠、刚性好和装卸方便等优点,但调整较费时间,很难在一次修磨中完成调整。
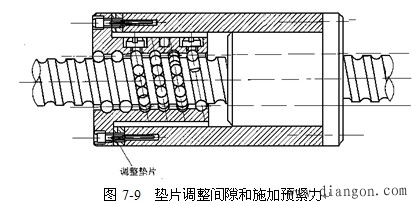 图7-10所示是利用两个锁紧螺母来调整螺母的轴向位移来实现预紧的结构,两个螺母靠平键与外套相连,其中右边的一个螺母外伸部分有螺纹。用两个锁紧螺母1、2可使螺母相对丝杠作轴向移动,在消除了间隙之后将其锁紧。这种调整方法具有结构紧凑、工作可靠、调整方便等优点,故应用较广。但调整位移量不易**控制,预紧力也不能准确控制。 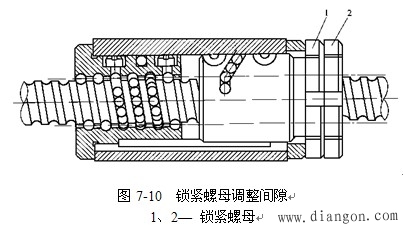 图7-11所示为双螺母齿差式调整间隙结构。在两个螺母的凸缘上分别切出齿数差为1的两个齿轮,这两个齿轮分别与两端相应的内齿轮相啮合,内齿轮紧固在螺母座上。预紧时脱开内齿圈,使两个螺母同向转过相同的齿数,再合上内齿圈。两螺母的轴向相对位移发生变化,从而实现间隙的调整和施加预紧力。这种调整方式的结构复杂,但调整方便,并可以获得**的调整量,可实现定量精密微调,是目前应用较广的一种结构。 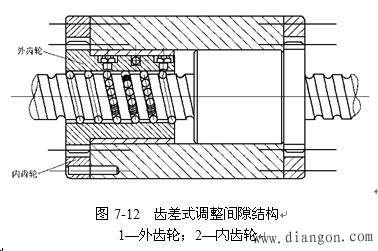 四、机床导轨 1.对导轨的要求 1) 导向精度高 无论空载或切削加工时,导轨均应有足够的精度 。 2) 耐磨性能好 导轨在长期使用过程中保持较高的导向精度。 3) 足够的刚度 导轨受力变形会影响部件之间的导向精度和相对位置,要求导轨有足够的刚度。 为减轻或平衡外力的影响,数控机床常采用加大导轨面的尺寸或添加辅助导轨的方法来**刚度。 4) 低速运动平稳性 要使导轨的摩擦阻力小,运动轻便,低速运动时无爬行现象。 5) 结构简单、工艺性好 导轨的制造和维修要方便,在使用时便于调整和维护。 2.导轨的种类和特点 (1) 滑动导轨 现代数控机床采用的导轨主要有带有塑料层的滑动导轨、滚动导轨和静压导轨。 滑动导轨有金属—金属型式,目前数控机床很少采用。多数采用金属——塑料型式,称贴塑导轨。 贴塑导轨一面贴有塑料板,采用特殊粘结剂加压固化,另一滑动面为淬火磨削面,快速运动可达30m /min。 滑动贴塑导轨的塑料化学稳定性高、摩擦系数低、静动系数差值小、耐磨损、耐腐蚀、吸振性好、比重小、强度大、加工成型简单,能在任何液体或无润滑条件下工作。 其主要缺点是耐热性差、导热率低,必须注意散热;热膨胀系数比金属大,应采用较薄的塑料板;在外力作用下易产生塑性流动;惯性差,应注意贴塑导轨的装配质量;吸湿性大,影响尺寸稳定性。 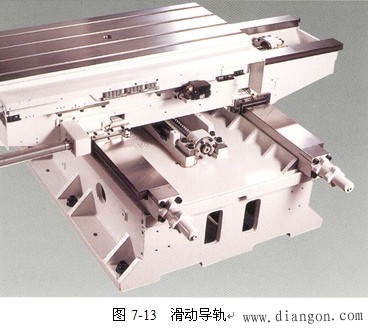 滚动导轨的特点是:摩擦系数小,摩擦系数一般在0.0025~0.005的范围内,动、静摩擦系数基本相同,启动阻力小,不易产生冲击,低速运动稳定性好;定位精度高,运动平稳,微量移动准确;磨损小,精度保持性好,寿命长;抗振性差,防护要求较高;结构复杂,制造较困难,成本较高。现代数控机床常采用的滚动导轨有滚动导轨块和直线滚动导轨两种。 1)滚动导轨块 滚动导轨块是一种以滚动体作循环运动的滚动导轨,其结构如图7-14所示。在使用时,滚动导轨块安装在运动部件的导轨面上,每一导轨至少用两块,导轨块的数目与导轨的长度和负载的大小有关,与之相配的导轨多用嵌钢淬火导轨。当运动部件移动时,滚柱3在支承部件的导轨面与本体6之间滚动,又绕本体6循环滚动,滚柱3与运动部件的导轨面不接触,运动部件的导轨面不需淬硬磨光。滚动导轨块的特点是刚度高,承载能力大,便于拆装。
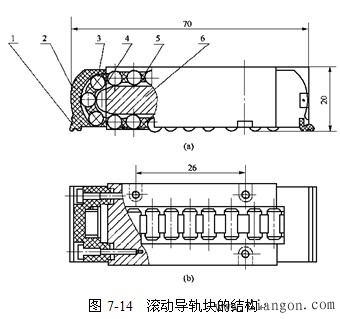 1—防护板;2—端盖;3—滚柱;4—导向片;5—保持器;6—本体 2)直线滚动导轨 直线滚动导轨的结构如图7-15所示,主要由导轨体1、滑块7、滚珠4、保持器3、端盖6等组成。由于它将支承导轨和运动导轨组合在一起,作为独立的标准导轨副部件由专门的生产厂家制造,故又称单元式直线滚动导轨。在使用时,导轨体固定在不运动的部件上,滑块固定在运动部件上。当滑块沿导轨体运动时,滚珠在导轨体和滑块之间的圆弧直槽内滚动,并通过端盖内的暗道从工作负载区到非工作负载区,再滚回到工作负载区,不断循环,从而把导轨体和滑块之间的滑动,变成了滚珠的滚动。
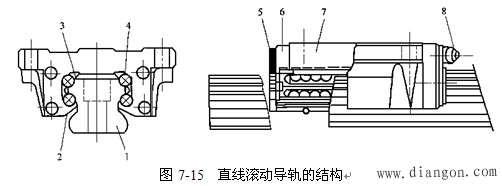 1—导轨体;2—侧面密封垫;3—保持器;4—滚珠;5—端部密封垫;6—端盖;7—滑块;8—润滑油杯 (3)静压导轨 静压导轨的导轨面之间处于纯液体摩擦状态,不产生磨损,精度保持性好;摩擦系数低(一般为0.005~0.001),低速时不易产生爬行;承载能力大;刚性好,承载油膜有良好的吸振作用,抗振性好;其结构复杂,需配置一套专门的供油系统,制造成本较高。静压导轨可分为开式静压导轨和闭式静压导轨两种。这里仅介绍较为简单的开式静压导轨。 开式静压导轨的工作原理如图7-14所示。油泵2启动后,油经滤油器l吸入,用溢流阀3调节供油压力,再经过滤油器4,通过节流器5降压至Pr(油腔压力)进入导轨的油腔,并通过导轨间隙向外流出,回到油箱8。油腔压力形成浮力将运动部件6浮起,形成一定的导轨间隙。当载荷增大时,运动部件下沉,导轨间隙减小,液阻增加,**减小,从而使油经过节流器时的压力损失减小,油腔压力Pr增大,直至与载荷W平衡。
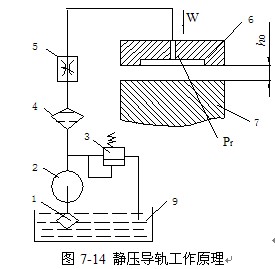 五、回转工作台 为了**生产效率,扩大工艺范围,数控机床除了沿X、Y和Z三个坐标轴的直线进给运动之外,往往还带有饶X、Y和Z轴的圆周进给运动。一般数控机床的圆周进给运动由回转工作台来实现。数控铣床的回转工作台除了用来进行各种圆弧加工或与直线进给联动进行曲面加工外,还可以实现**分度,这给箱体零件的加工带来了便利。对于自动换刀的数控机床来说,回转工作台已成为一个不可缺少的部件。数控机床中常用的回转工作台有数控回转工作台和数控分度工作台两种。 |